Case Flow Rack
The Case Flow Rack system, also called Carton Live Storage (AR Carton Flow), permits high density storage of cases and light products, leading to savings in space and improved stock turnover control.
AR Racking is proud member of these national associations:
The Case Flow Rack system has a slight slope on the platforms that enables the sliding of the products that enter the racking from one end to the other, thus reducing distances travelled in the warehouse and saving operations time, so it is perfectly adapted to warehouses with a large volume of manual picking operations.
These gravity-fed racking systems are commonly used in warehouses to improve the efficiency of order picking for small items or lightweight cartons.
They are also designed to work with the FIFO (First In, First Out) warehouse management method, ensuring excellent product rotation and minimizing potential bottlenecks. With separate areas for loading and unloading, this system is an unbeatable solution for managing products with a high turnover rate.




How does it work?
Case Flow Rack - AR Live storage (Picking)
Case Flow Rack system is a gravity system with slightly sloped platforms or roller beds where the goods are placed at the higher end and move to the other through gravity, with those goods previously stored on the racking being the first ones to exit at the opposite end. This operation allows FIFO (First in, First out) stock management.
When the first carton is removed, the others automatically slide towards the operator’s position, allowing a large number of items to be stored in the same bay.
This storage system is perfect for companies and organizations with high picking volumes. It boosts the number of lines and speeds up the order preparation process, while also reducing handling costs and operator movement within the warehouse.
The rails can be easily adjusted crosswise to accommodate different unit loads, making it a highly versatile system for picking.
Advantages
Case Flow Rack advantages and features:
These are the main advantages of the case flow rack system:
- Exploitation and optimization of available space in the warehouse. High-density storage system, i.e., the same space but with more storage capacity.
- Perfect product rotation: When implementing the FIFO (First in, First out) system, the first unit load in is the first one out.
- With no passageway obstructions, either in replenishment or order preparation tasks, because the unit loads are placed and removed on different aisles, as the loading and unloading aisles are separated.
- Compatible and combinable with other AR Racking storage systems.
- It allows for the possibility of adding aisles with height levels and installing selective pallet racking on the upper levels.
- Adaptable to different sizes and shapes of cartons and light loads. The slope and the distances between pulley rails can also be modified, while the height and angle of inclination is adjustable too.
- Simple and quick installation. The installation does not require subsequent maintenance either.
- It increases the profitability of the warehouse, reducing operator handling and movement times due to the higher number of references at the front of the racking, meaning shorter distances.
- Quick and simple removal. The manual handling and removal time of unit loads is reduced due to the good location of the products.
- Possibility of simply installing order preparation systems with WMS (Pick to light) integrated in the actual storage solution.
Main applications of Case Flow Rack Solution
This storage system is designed for companies that have a very high volume of picking and high quantity of homogeneous products, and ensures perfect product rotation and warehouse optimization.
- These types of solutions are implemented in a very wide variety of sectors: from warehouses for consumer goods, such as pharmaceutical and cosmetics products, to computer products, automotive components, etc.
- Case Flow Rack is popular in consumer product sectors such as the food sector due to the importance of expiry dates.
- It is a very commonly used storage system in warehouses and distribution centres for components for the automotive sector.
- They are suitable storage systems for storing small or light items of any size, mainly for picking or order preparation of small loads.
Components and accessories
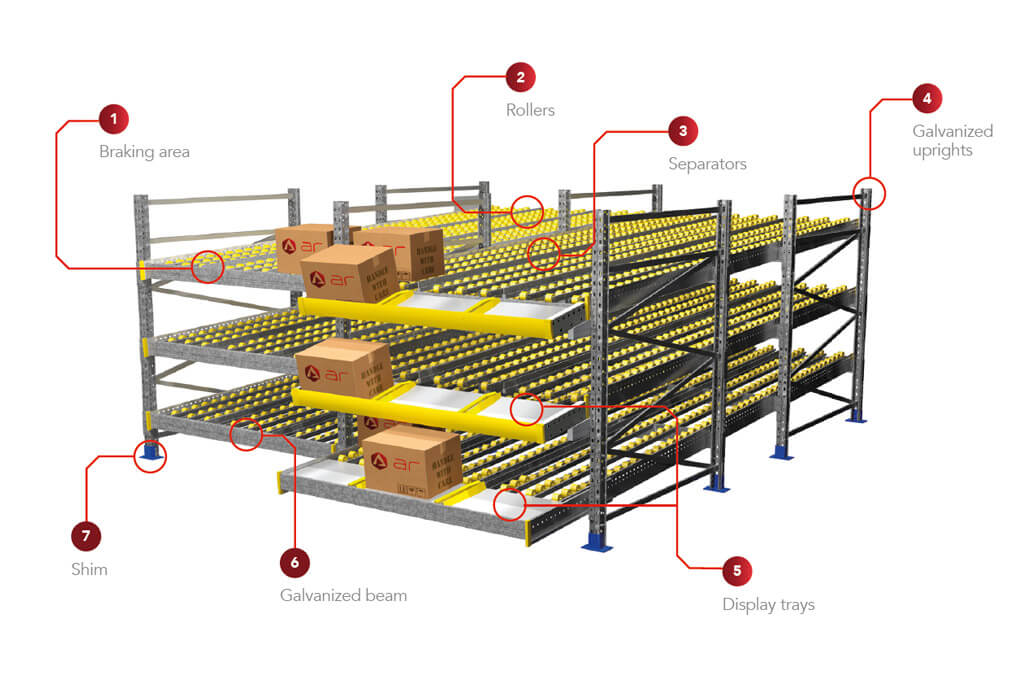
Case Flow Racking Components and Accesories:
The Case Flow Rack system is designed to meet a wide range of storage needs, specifically for picking operations. It features a base frame that includes entry and exit profiles, side profiles, and guide rails.
The system also offers a variety of adjustable or optional components, allowing it to be customized for the specific requirements of each installation or industry. These components include display trays, straight platforms, separators, braking systems, and more.
Frame elements in Case Flow Rack system
Frame
The main function of the frame is to support the load levels of a bay, consisting of two vertical uprights, plus the diagonal profiles, base supports and corresponding accessories.
It consists of two beams joined together by a series of side safety pins.
Shim
The shim is a component located under the frame support in direct contact with the floor if it is uneven, to ensure the correct levelling of the entire structure.
This guarantees that the structure is well balanced and levelled, which is essential for safe operation.
Galvanized upright
The upright is the main component of the frame, and is galvanized, which provides support and stability to the structure.
It is a component that forms the vertical structure and helps withstand the load that it supports. Its design will depend on the load capacity that the racking has to support.
Beams for Case Flow Rack Solution
Galvanised beam
The beams are metal components attached directly to the frames. They are the horizontal elements that connect to the uprights and act as support for the racking pallets on which the stored products are placed.
They are manufactured in different lengths and widths according to the load capacity required and are adjusted between the uprights to define the horizontal distance between the racks and trays. They are also responsible for distributing the weight of the loads evenly.
Specific elements of Case Flow Rack Solution
Braking area
The braking area may consist of different types of devices, such as special wheels or rollers that provide resistance to product movement. They can also include specific speed control mechanisms.
This component is placed at the end of the rail and is used for product braking and control, preventing its impact against the outflow profile.
Reducing the speed of the products before the presentation area facilitates the picking process and minimizes the risk of accidents or damage to the products.
Rails
Metal components that have in their interior a set of wheels, pulley wheels or rollers that allow the sliding of the load.
Rollers
This is one of the most important components of the carton case flow rack system. Its main function is to slide the load placed on the racking thanks to a slight slope in its structure.
This component may also consist of wheels, fulfilling the same function.
Dividers
They are metal components used to divide and organize the products into different channels in the racking.
These dividers are essential to maintain the order and facilitate the identification and removal of products during the picking process. They also serve to help the operator to place the load on the racking.
Presentation trays
These are tray-shaped flat surfaces located at the front of the sloped channels. These trays play an important role in the order preparation process, as they provide an easy to access and visible space for the products that are ready to be selected.
The presentation trays also act as a waiting area for the products that are at the front of the channels.
Once an item has been removed from the presentation tray, the goods behind it will occupy its place, thus maintaining a continuous flow of unit loads ready to be selected.
These trays can be tilted to facilitate the removal of the products that are stored inside a carton.
Possibility of combination with other systems
One of the great advantages of Case flow rack is its simple adaptation in combination with other pallet storage systems.
The installation at lower levels of Carton flow rack systems enables the installation of other systems at higher levels, as shown below:
- PUSH-BACK RACKING
- SELECTIVE PALLET RACKING
- FIFO LIVE PALLET RACKING (First in, First out)
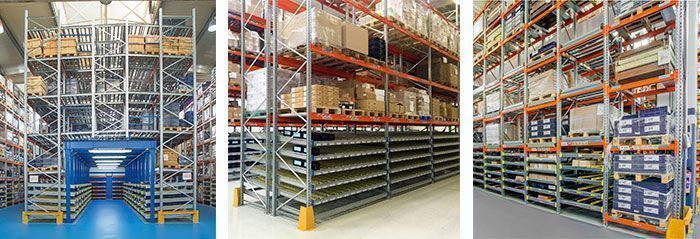
Quality and Safety
Case Flow Rack systems comply with the strictest National safety standards, and also come with AR Racking’s quality and innovation guarantee.
5-year quality guarantee
The confidence in our Carton Case Flow systems means we are able to offer 5-year quality guarantees against all types of manufacturing or hidden defects in the main structural components.
Component traceability system
Since 2016, the main components of our racking systems have included a component traceability system.
With this system, the different components have an identifying marker, which means knowing and having documented each piece from source without needing to have the package label and, therefore, knowing the exact component, how it was designed or what raw material was used in its manufacture.
Fully automated manufacture
The production process of our industrial racking systems is fully automated: it incorporates latest generation profiling machines with continuous cutting process and laser measurement control, welding centres, painting and packaging processes, all fully automated, guaranteeing the highest quality parameters.
Designs in the R&D&I Centre
Our Carton Case Flow systems are designed in our technology centre dedicated exclusively to R&D&I activities, as well as with the advanced engineering projects development area, which allows us to respond appropriately to more demanding logistical requirements.
Tests at Research and Testing Laboratory
With the creation of our Research and Testing Laboratory, together with the University of Mondragón, our technical area continuously tests and analyses products and materials to optimize our industrial racking.
It simulates, calculates and researches (with specialised software) the efficiency of the geometries, and makes full structural calculations on the behaviour of systems already installed in different situations.
Quality certificates in Case Flow Rack System
- ISO 9001: 2008
- ISO 18001: 2004
- OSHAS 18001: 2007
- Welding certificate: UNE EN ISO 3834-2: 2006
- Resistance of galvanised steel certificate: UNE-EN ISO 14713-1
- Reaction to fire of galvanised steel: EN 13501-1: 2007
References
References
With over 26,000 storage projects completed in more than 60 countries, we are leaders in industrial racking solutions. We are proud to have collaborated in the optimization of warehouses with picking solutions for international companies from diverse sectors.
Some notable projects include:
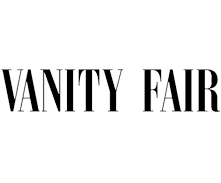
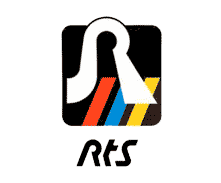
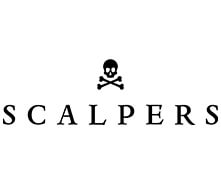
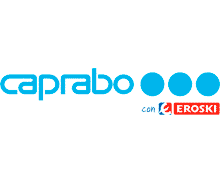