Shuttle Pallet Racking
The Pallet Shuttle Racking (AR Shuttle) is a high-density compact storage solution that uses powered shuttles to automatically carry loads into the rack.
The pallet shuttles are remotely controlled by an operator.
AR Racking is proud member of these national associations:
Hence, there is an optimum use of storage space and workplace accident rates are also reduced.
The use of automated shuttles in place of forklifts during the storage process not only reduces the risk of accidents, but also the maintenance costs resulting from damage of the rack.
This system can work either as FIFO or as LIFO, even in freezer chambers, with temperatures of up to -30°C.
This pallet shuttle system reinforces logistical capacity qualitatively and quantitatively, since it automates the handling of goods on pallets; it is also possible to control the inventory through a system of sensors which count the stored pallets.




How does Shuttle Pallet Racking work?
The Pallet Shuttle Racking is a compact semi-automated pallet storage solution using self-powered shuttle carts which operate independently to move the pallets in the rack.
Designed for high-turnover storage, this solution enables automatically loading and retrieving pallets continuously by using a remote controlled system.
Unit loads are either placed on the first available location until the rack is fully loaded, or retrieved from their storage locations and moved to the front ready to be picked by a forklift truck, until the rack is fully unloaded.
AR Shuttle is positioned in the lane required with a forklift truck. The pallets are stocked one by one by the forklift truck at the beginning of the lane.
The pallet shuttle lifts up the platform and moves it along the channel until it reaches the first free position, where it puts the pallets. Then, it comes back to the beginning of the lane ready for the next drive cycle.
The Pallet Shuttle system enables warehouse operation through both FIFO and LIFO management, with the latter being more common due to only using one of the ends of the aisle for loading and unloading pallets.
For FIFO operation in the Pallet Shuttle Racking System, forklift access must be enabled at the end of the level, therefore allowing access to the unit load located at the back.
This will make it possible to complete the FIFO stock management cycle, and the first pallet to enter the structure will be the first one out. Before putting the last pallets into the lane, AR Shuttle must be removed and put in a new lane.
Advantages of the Shuttle racking
The main advantages of the AR Racking Inc Pallet Shuttle system are its racking compaction capacity and the increase in productivity and safety in the warehouse.
- The Pallet Shuttle system enables you to maximize floor space and height available by minimizing the operating aisles needed for trucks.
- The AR Shuttle system allows for automatic control of inventory by using sensors to count the number of pallets stored.
- Remote control and bar codes help better control the stock, drastically decreasing error margins.
- Since forklift operators do not have to enter the aisles, maximum safety is guaranteed when handling pallets, avoiding collisions in the rack structure. This reduces maintenance costs as well as the number of issues from handling loads.
- With the pallet shuttle system, stored pallets can be loaded and unloaded as FIFO or LIFO, even in freezing chambers up to -30ºC.
- Optimization of space FIFO / LIFO
- Enables a continuous handling flow, speeding up operations in the warehouse.
- Constant handling flow.
- Powered by a rechargeable lithium battery.
- Highly safe operation at low maintenance cost.
- RF controlled.
- Flexible storage for different types of pallets
Main applications of Warehouse Shuttle Systems
Semi-automated Pallet Shuttle Racking is a system that optimizes space and productivity in the warehouse.
Its main applications are therefore:
- Warehouses with high loading and unloading activity, and which therefore require high warehouse productivity.
- Warehouses with a reduced number of product references, but a high volume of pallets.
- Warehouses with seasonal merchandise, which require fast and flexible operations in specific time periods.
- Warehouses with cold rooms or freezing chambers, due to the maximum compaction of the space this allows, together with the time saving for the loading and unloading of pallets.
- Due to its dual FIFO and LIFO management capacity, it can be suitable for warehouses with both perishable and non-perishable products, depending on the chosen configuration.
Components and accessories of the Shuttle Pallet Racking System:
The Pallet Shuttle Racking storage system consists of a basic structure of frames and beams with the quality characteristics of all AR Racking’s racking solutions.
This system also has specific components that allow their semi-automatic operation, mainly the shuttles and the rails on which the shuttles move. Safety accessories are also added for the structure and the unit loads.
We divide the main pallet shuttle racking components between the metal structure and the shuttles themselves.
Components of the pallet shuttle structure:
Galvanized frame
The galvanized frame, as in other storage systems, is one of the basic components of the racking and consists of 2 galvanized uprights or columns, their diagonals, baseplates and floor fixing elements.
Beam
This is a horizontal component that joins the frames together and supports the load. In pallet shuttle racking the rails are supported on the beams and enable the horizontal movement of the shuttles.
The beams are joined to the frame by connectors in the drill holes of the upright.
Rail supports
This is the component that supports the metal rails on which the pallet shuttle moves.
The external supports are anchored to the entry and exit uprights of each aisle, while the internal supports are anchored to the beams.
Shuttle rails
This is the metal component that enables the movement of the pallet shuttle along the aisle. It is supported on the beams and its corresponding supports.
Pallet guidance
It is situated at the start and end of each level, on each side of the lane, to facilitate the task of depositing the unit loads and prevent them from veering from their correct course.
Rail backstop
Component located at the end of the lane, in the unloading area whose purpose is to inform the shuttle of the end of the rail and activate its braking and stopping system.
Pallet Shuttle Racking shuttle components
Shuttle for pallets:
Pallet Shuttle Racking shuttles consist of a base platform equipped with wheels to enable their movement.
A pallet lifting system on the shuttle itself, and a long list of sensors and detection readers that collect information from their environment and implement safety measures.
The shuttle itself is provided with different status indicators, to inform the operator of any possible error, the battery level or whether it is on or off.
Pallet Shuttle remote control:
This is the basic control device of Pallet Shuttle Racking which the operator uses to indicate the required operating capacity. It is simple to use with the control buttons and has an information screen.
- Each remote control unit can control up to 4 pallet shuttles.
- Pallet count command.
- Onscreen messages far machine maintenance.
Types of pallets stored by the AR Shuttle
- Europallets
- Industrial pallets
- Pallets for the chemical industry
- Pallets for the food industry
In the Pallet Shuttle system pallets can be stored and retrieved according to two different storage orders:
LIFO (Last-in-First-out)
This is the most common system, where the pallets are put in and taken off from the same side.
The lanes should be completely emptied before putting in a new load.
FIFO (First-in-First-out)
This system is ideal for buffering units or transit warehouses, where incoming and outgoing operations are performed from opposite sides.
When the lane is not completely emptied, fast relocates the pallets by bringing them closer to the exit position, allowing new loads to be placed on the rack.
Depending on the required functionality, Shuttle will come equipped with the following elements:
Standard functionality
- Charging
- Continuous charging
- Unloading
- Continuous unloading
- Unloading by quantity
- LIFO pallet compaction
- Pallet compacting FIFO
- Pallet counter
Standard equipment
- On-board lithium battery
- Battery charger
- Remote control
- User manual
Optional equipment
- Multipallets
- Spare parts
- Cold room version
Quality and security Shuttle Pallet Racking
Pallet Shuttle Racking complies with the strictest national safety standards, and also includes AR Racking’s guarantee of excellence.
Five-year quality assurance
The reliability of our pallet racking solutions means we are able to offer 5-year quality guarantees against all types of manufacturing or hidden defects in the components of the main structure of our racking solutions.
100% automated production
The production process of the basic components of our Pallet Shuttle Racking solutions is fully automated in our production centre: state-of-the-art profiling machines with a continuous cutting process and laser measurement control, welding centres and automated painting and packaging processes, which guarantee the highest quality parameters.
Traceability system
Our industrial pallet racking uprights and beams include a pioneering traceability system in the sector. With this system, our storage system components have an identifying mark, which means that each upright and beam can be traced and documented, and that information is therefore available on its design and the raw material used in its manufacture.
Designs developed at the in-house technology center
Our Pallet Shuttle Racking systems are designed and calculated in our exclusive technology centre where our expert technical team allows us to develop projects with diverse and demanding logistics requirements.
Tests at Research and Testing Laboratory
The Research and Testing Laboratory developed in collaboration with a prestigious university allows us to test and analyse our Pallet Shuttle Racking systems; it simulates, calculates and researches the efficacy of the geometries, and makes full structural calculations on the behaviour of systems already installed.
The quality certificates of the Pallet Shuttle (AR Shuttle) are:
- ISO 9001: 2008
- ISO 18001: 2004
- OSHAS 18001: 2007
- Welding certificate: UNE EN ISO 3834-2: 2006
- Galvanized steel corrosion resistance certificate: UNE EN ISO 14713-1
- Galvanized steel reaction to fire: EN 13501-1: 2007
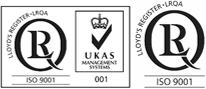
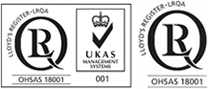
Our experience in optimizing our customers’ warehouses comprises more than 26,000 projects carried out in over 60 countries.
And with customers from various sectors: Food and beverage, automotive, distribution, electronics, pharmacy and cosmetics, industrial and transport and logistics.
Below are some examples of Pallet Shuttle Racking projects:
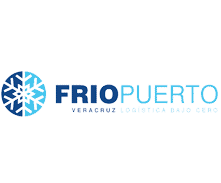
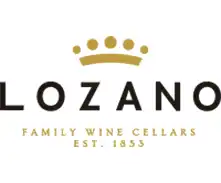
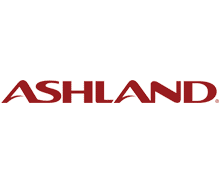
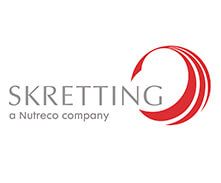
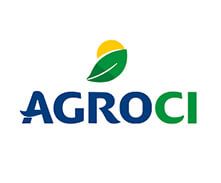