The manufacturing process is the process that aims to transform a raw material into a finished product, complying with the required quality and safety requirements. For manufacturing to be competitive, it is important that the cost of the material, the manufacturing and the storage of the final product are as profitable as possible.
The manufacturing process is inherent to the industrial sector, but how exactly is the manufacturing process of the main industrial racking components? How are the beams and uprights that make up the structure of the storage systems mostly manufactured?
Racking Production Process phases: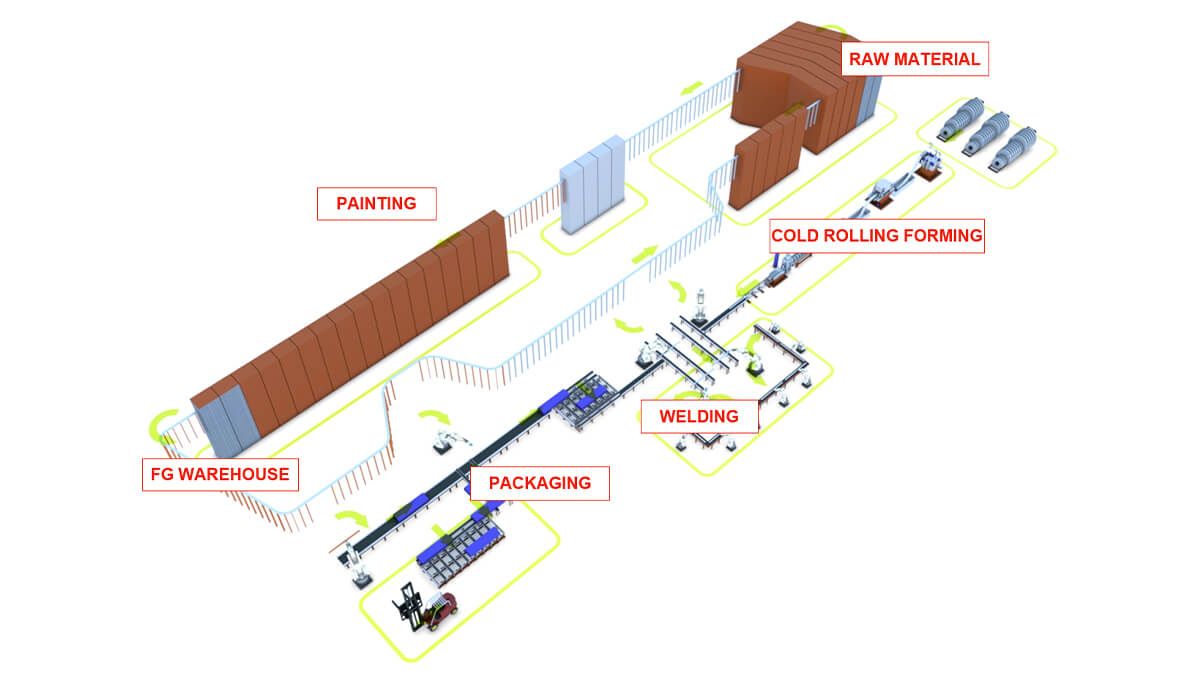
Raw Material of Industrial Racking
In the case of industrial racking, knowledge of the raw material, in this case steel, is key because it provides the basis for using the appropriate quality of raw material for each product.
To manufacture storage system components and according to each of their requirements, different grades of steel are used in accordance with the following standards:
- EN 10025: Hot rolled steel products for structures.
- EN 10346: Continuously hot-dip coated steel flat products. Technical supply conditions.
- EN 10149: Hot rolled flat products made of high elastic strength steel for cold forming.
- EN 10139: Low carbon steel strips, uncoated for cold forming.
Profiling process
In this phase, a machine that produces rolled steel with advanced, robust and versatile technology will help, through strict control of the profile dimensions, to ensure that the product is always within the established quality parameters.
In a high quality and demanding profiling process, a full list of dimensions must be defined for each manufactured article (beams and uprights in this case), which is continuously checked during each production order. Each critical measurement must be controlled to ensure the correct behaviour of the product, both in the assembly of the installation and under the application of the load.
In this part of the process, some industrial racking manufacturers implement a traceability process in their components, identifying each component with a serial number that makes it unique and easily identifiable.
Product traceability system is a process encompassed within the so-called Industry 4.0 philosophy. To discover all the keys, please read our post on product traceability applied to industrial racking.
Welding process
The weld between the profile of the beam and the connector is one of the critical components of the industrial racking system. The automated manufacturing system provides uniform welding with an excellent surface finish. Subsequently, if final control is carried out of all the welded components, any possible defect in this operation is discounted.
For industrial racking systems, the welding process must comply with the ISO 3834-2 regulations on Quality requirements for the fusion welding of metal materials.
Finish of the racking components
The beams, uprights and frames must best adapt to the customer’s needs, the product characteristics and/or environmental conditions. Consequently, the uprights and beams can have one of the following finishes:
- Pre-galvanised upright:
For those components which are more difficult to replace such as uprights and which are more exposed to scratches. The pre-galvanised finish guarantees optimum resistance.
- Paint finish:
The beams can be both pre-galvanised and have a paint finish, thus increasing the visual contrast with respect to uprights and diagonals and therefore facilitating the work of the forklift driver.
In cases in which the beams and some other accessories require a paint finish, an automatic process will be implemented, where they receive prior to the degreasing phase a treatment with a nanotechnological product of synthetic ceramic compounds and washing with 100% osmosed water. This eliminates the possibility of the appearance of impurities which can cause corrosion.
The paint is poured through an electrostatic application in an automated booth. For this reason, it is sprayed with epoxy-polyester followed by oven compaction. Industrial racking that meets the highest quality parameters usually has the a2 - s1, d0 paint certification according to UNE EN ISO 13501 which regulates the fire reaction and resistance properties of construction products and building elements.
- Hot dip galvanised beams:
The beams can also be produced with a hot-dip galvanised finish, whose main characteristic is its high resistance in extreme conditions, since the main advantage of hot-galvanising a component is to avoid rust and corrosion that humidity and environmental contamination can cause industrial racking steel components.
Packaging of uprights and beams
It is the final phase of the racking manufactuing process and is generally also automated to ensure a uniform finish with excellent protection against accidental impacts during the handling and transport phases.
In this phase the uprights and beams are stored in packages. Subsequently, each package is packed with plastic, ensuring that the products arrive protected to their destination, avoiding damage to the material during handling and transport. Finally, the packages are arranged together for storage and delivery, using polyester strips.
Product storage
Finally, the finished product must be temporarily stored in a facility close to where the manufacturing process is carried out. The stock management of the finished product may vary according to the company, type of product or external factors affecting the market at the time.