We know what key aspects must be considered when ensuring safety in a warehouse and we have previously discussed the risks and prevention measures associated with industrial racking systems to be adopted to ensure the safety of an installation in a logistics centre.
All storage solutions provided by AR Racking include a full 5-year guarantee to give its customers greater peace of mind when using their facilities.
There are some general guidelines that all companies should consider for the correct maintenance of a racking system.
Inspection plan for maintenance of industrial racking systems
An adequate maintenance programme for all the installations must be implemented, with it being advisable that this is carried out by the actual manufacturer of the racking or according to their specifications.
Establishing a periodic racking inspection plan is important for the detection, communication and recording of any easily visible anomalies:
Daily visual inspection of the racking:
- Who: warehouse personnel.
- Objective: detect easily visible anomalies in the industrial racking (deformed beams or frames, cracks in the floor, breakage of anchor bolts, etc.)
Weekly inspection:
- Who: warehouse supervisor.
- Objective: check the lower levels of the racking (1st and 2nd) for any anomalies.
Monthly inspection of the racking:
- Who: warehouse supervisor.
- Objective: check every level and general aspects of order and cleanliness of the structure.
Annual inspection by expert:
- Who: personnel who are independent, competent and experienced in the activity.
- Objective: detailed notification, assessment and communication of damage.
How to perform a warehouse racking inspection
Technical inspections are a fundamental requirement for the correct functioning of the storage solutions and to ensure safety.
How should they be performed and what steps should be followed in this process?
Inspection of racking overloading damage:
- Maximum sag L/200
- For L=2700 mm -> d=13.5 mm
- For L=3600 mm -> d=18 mm
Inspection of safety pins
- If they are missing they must be put back immediately.
Inspection of damage on racking uprights and latticework (basic level of inspection)
- 3 mm at upright depth
- 5 mm upright side
- 10 mm diagonal
Based on the above-mentioned parameters and the results obtained in the industrial racking inspection, the levels of risk and measures to adopt are as follows:
- GREEN RISK: Deformations less than those indicated above. The industrial racking only requires monitoring.
- ORANGE RISK: Deformations more than those indicated above and less than twice as much. Actions are required to the racking as soon as possible (4 weeks before scaling up to the red risk).
- RED RISK: Deformations more than twice those indicated above. Unload and isolate the racking immediately. The damaged component must be replaced.
Replacement of damaged components on an industrial racking system
If in the inspection process for the maintenance of industrial racking systems the results indicate a red risk, the damaged racking component will need to be replaced as soon as possible.
And why replace and not repair the damaged racking component?
This is explained in the UNE 58013 standard:
- Industrial racking repairs are not recommended and must be approved by the design manager, i.e. the racking manufacturer.
- When carrying out repairs it is prohibited to use either the application of heat (torches, welding) or cold forming as the mechanical characteristics of the racking steel would be altered.
- Structural components with major damage cannot be repaired and must only be replaced.
- The new component must be identical to be replaced one.
All risk prevention standards and recommendations must be followed to replace a damaged racking component. The following general specifications must be applied:
- According to UNE EN 15635: unload the industrial racking before replacing/repairing any component.
- Some work must be carried at height (changing a beam, replacing a pallet backstop, etc.). For this, suitable mechanical and safety equipment such as platforms, harnesses, etc. must be used.
- Illuminate the area/walkway being worked in to avoid tripping, the falling of tools from height or the platform from overturning.
The procedure to replace the different components of an industrial racking system is similar, but each one has its specific characteristics.
Replacing a beam on an industrial racking system:
Unload the whole bay.
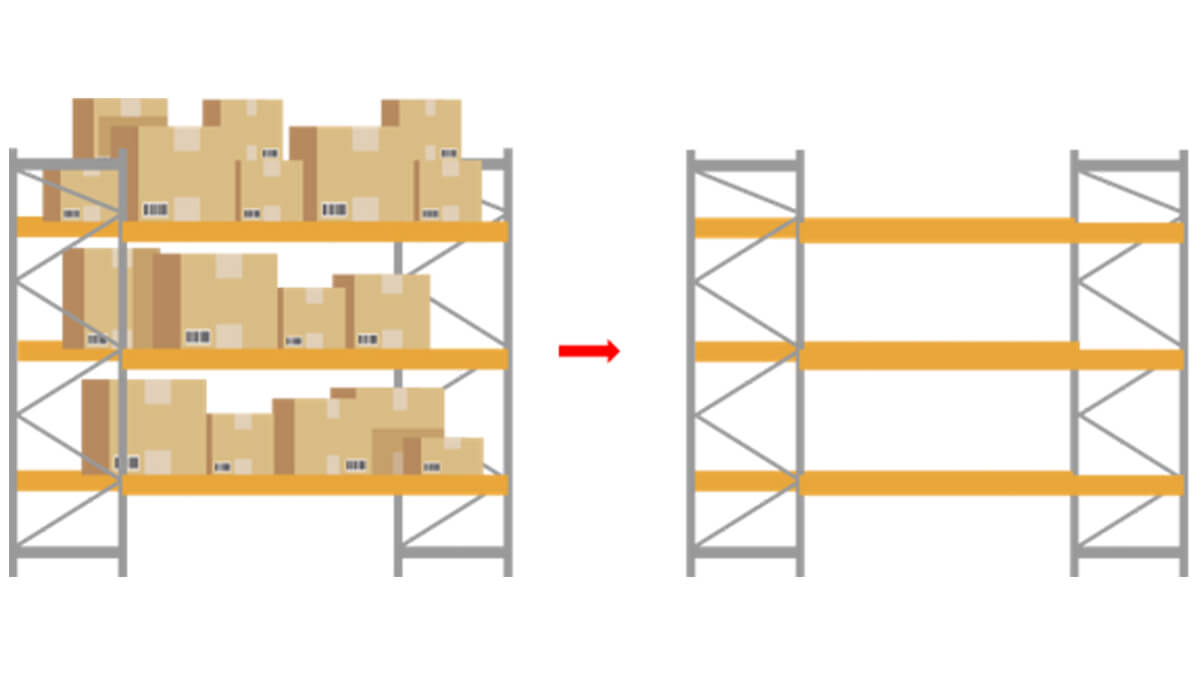
Remove the safety pins of the beams to be replaced.
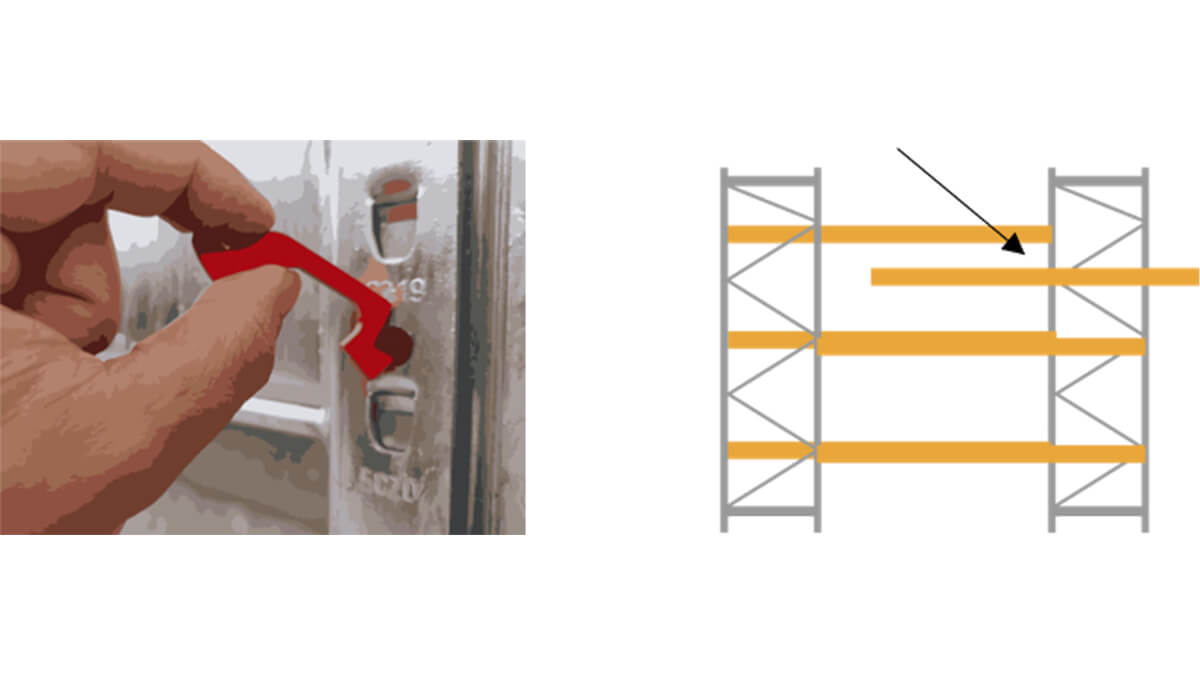
Mount the new beam and insert the safety pins.
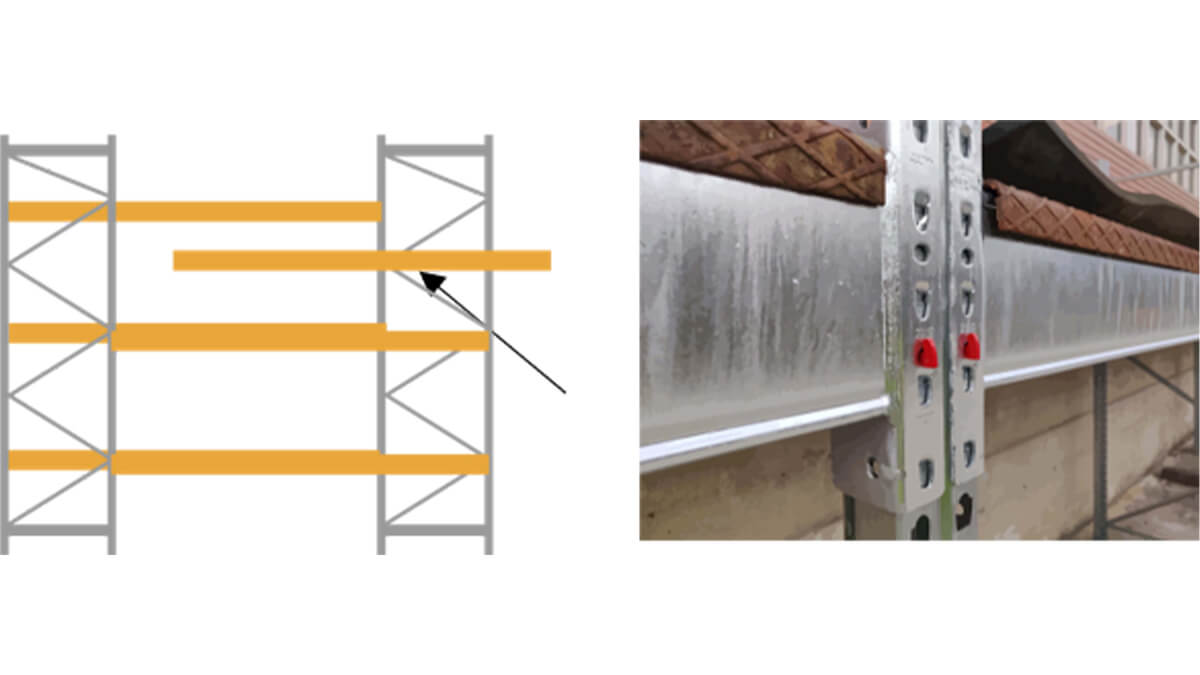
Only one beam can be removed at a time. If in the same bay there is more than one damaged beam, replace sequentially. One by one. Do not remove more than one racking beam at a time.
Replacing a racking upright or frame protector:
Unload the bays adjacent to the protector.
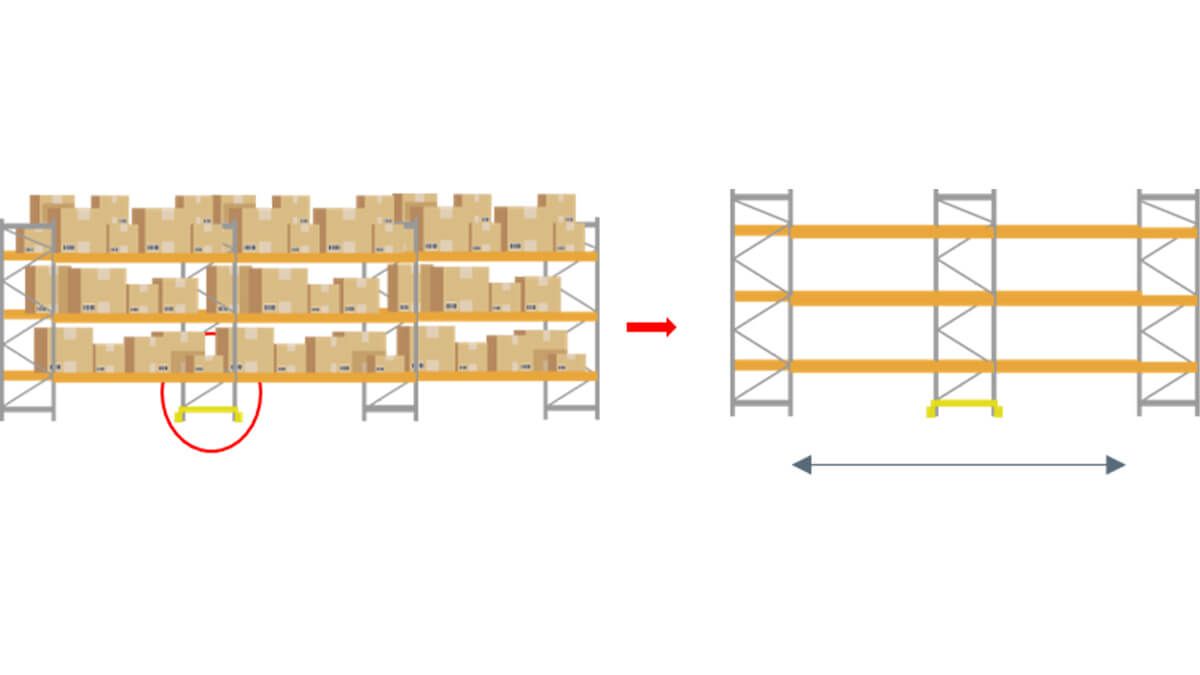
Remove the damaged protector.
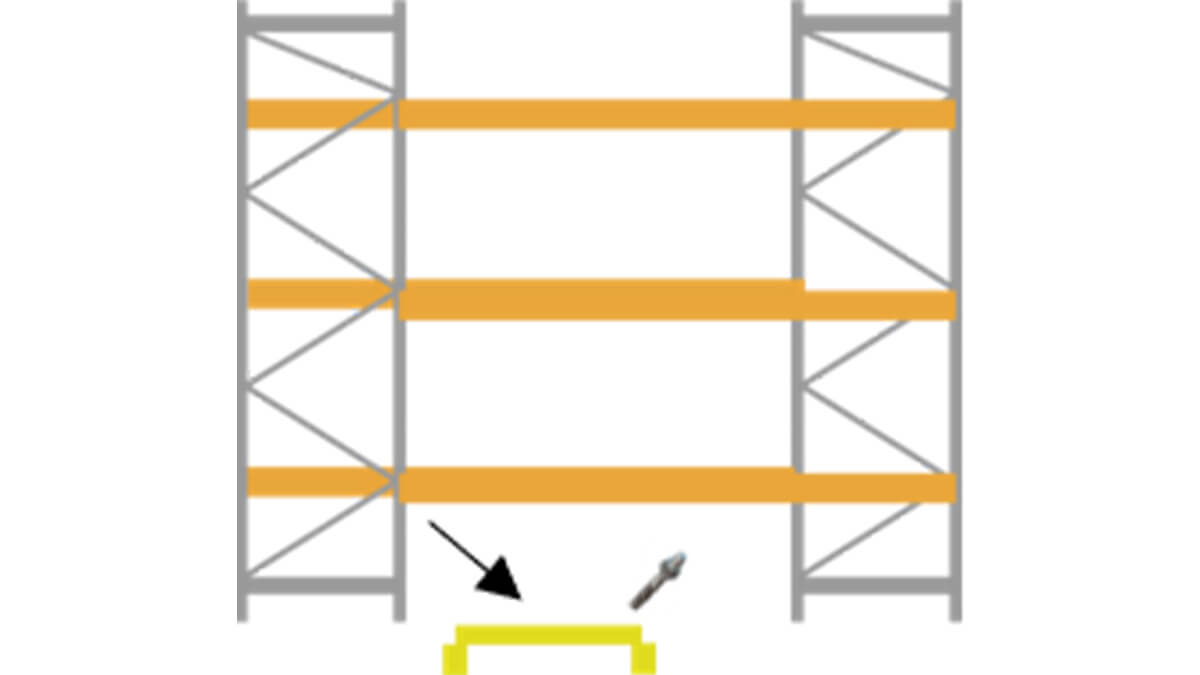
Check that the anchor bolts are not damaged and that there are no cracks on the floor. If the anchor bolts are bent or there is any defect in the floor, please contact the industrial racking manufacturer.
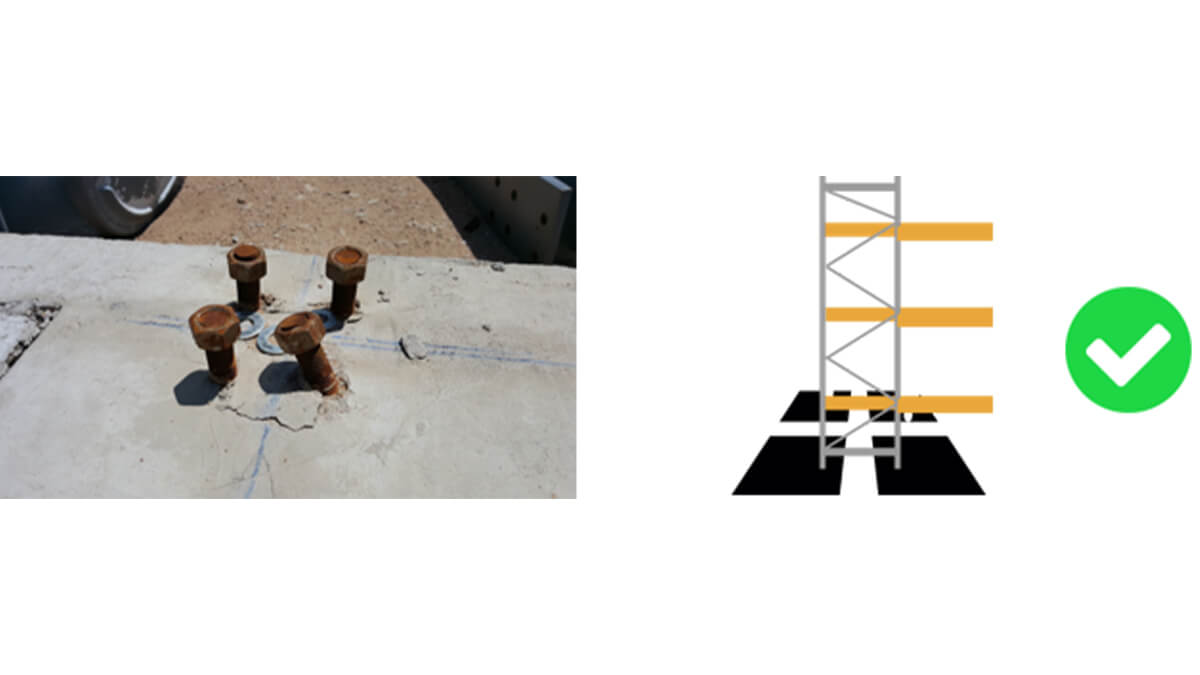
Mount the protector on the installed anchor bolts.
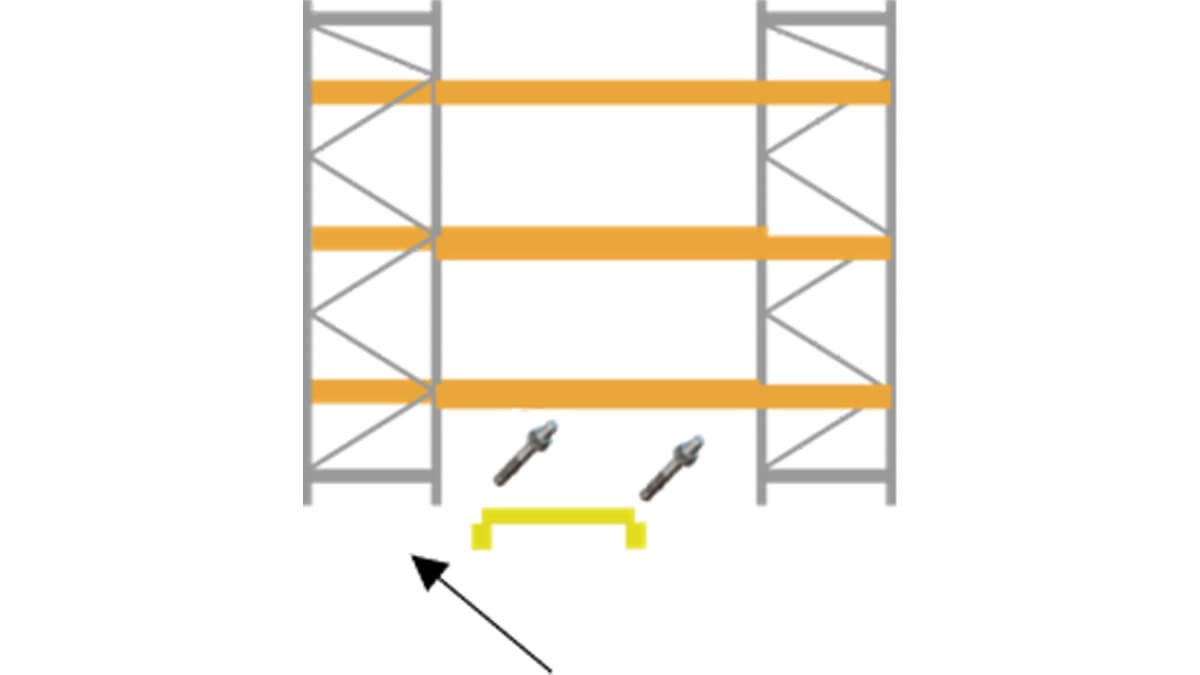
Replacing a diagonal profile in the storage system:
Unload the bays on both sides of the affected frame.
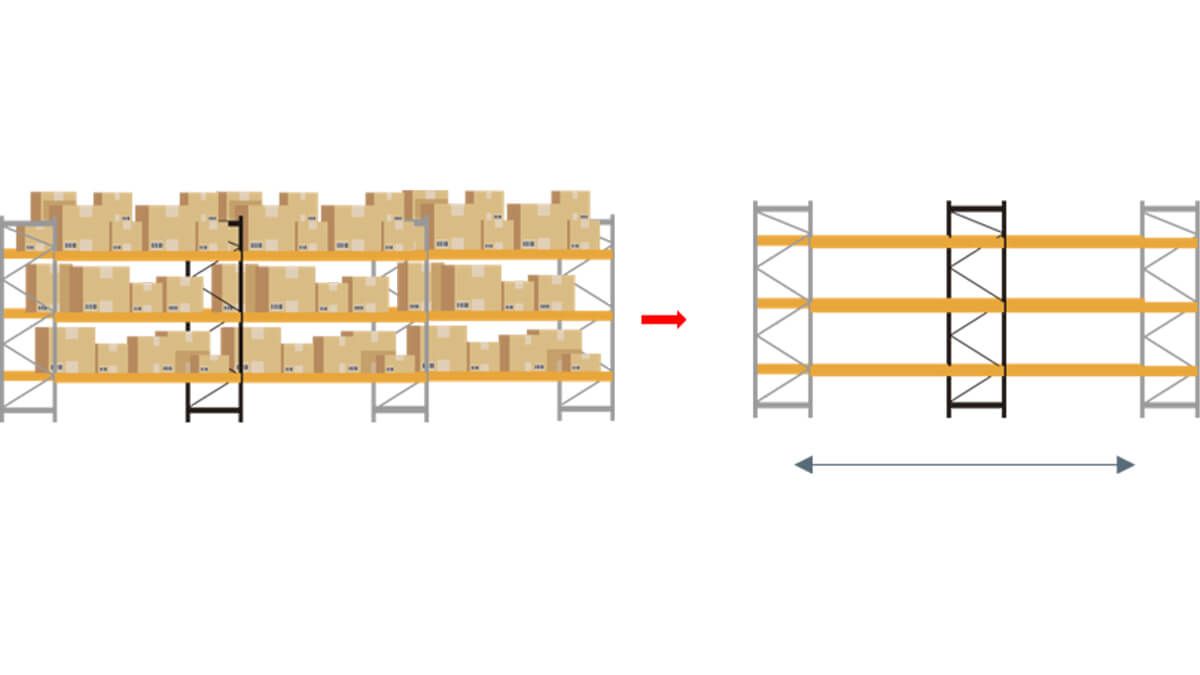
Loosen the screws and remove the damaged diagonal of the racking system.
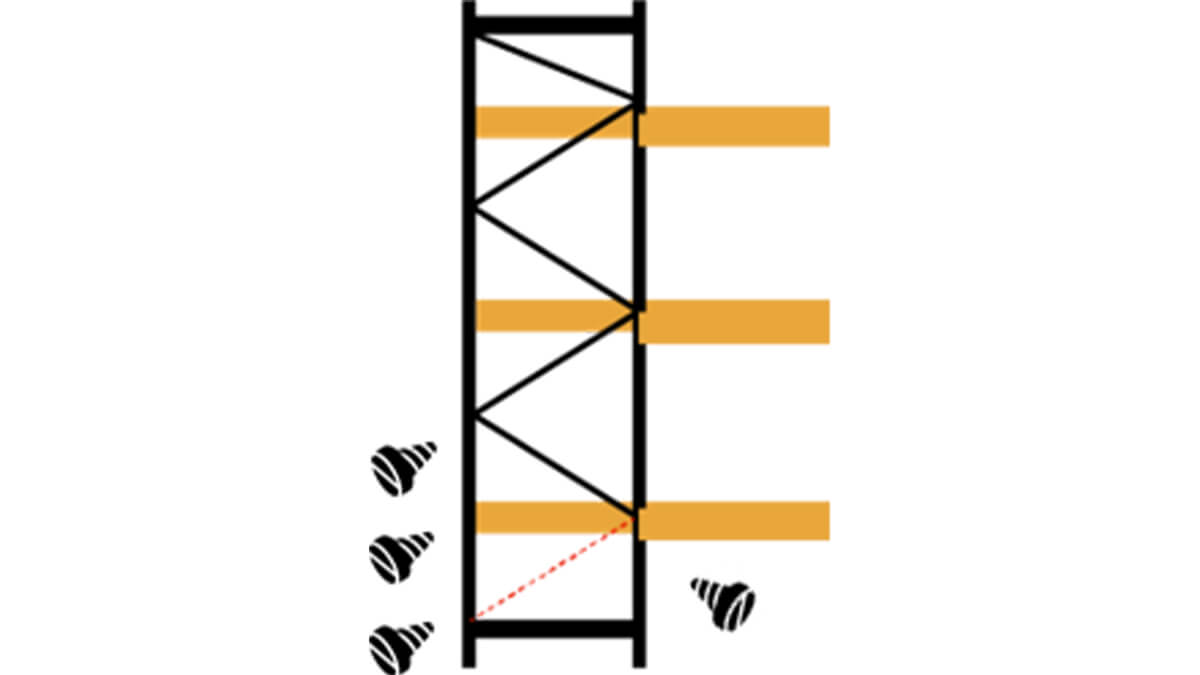
Check for any damage on the upright (worn hole). If there is any damage on the upright it must be replaced. If in doubt, always contact your industrial racking supplier.
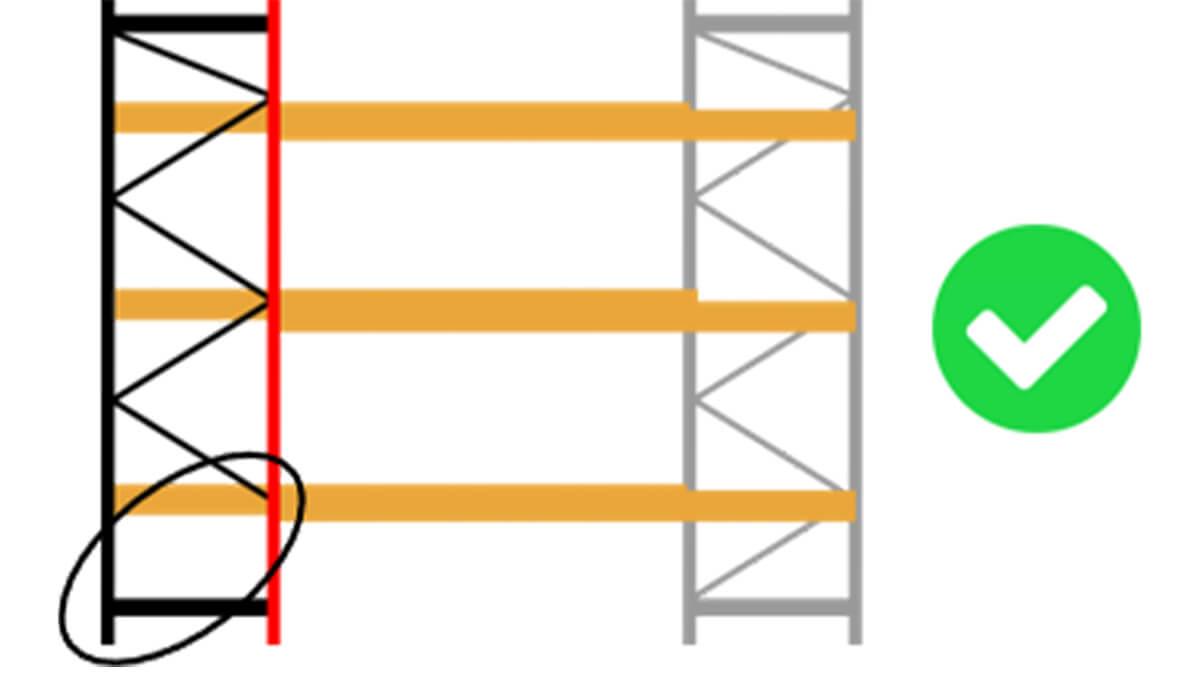
If the upright is not damaged, mount the diagonal and tighten the screws with a maximum torque of 20N·m (to avoid deforming the diagonals).
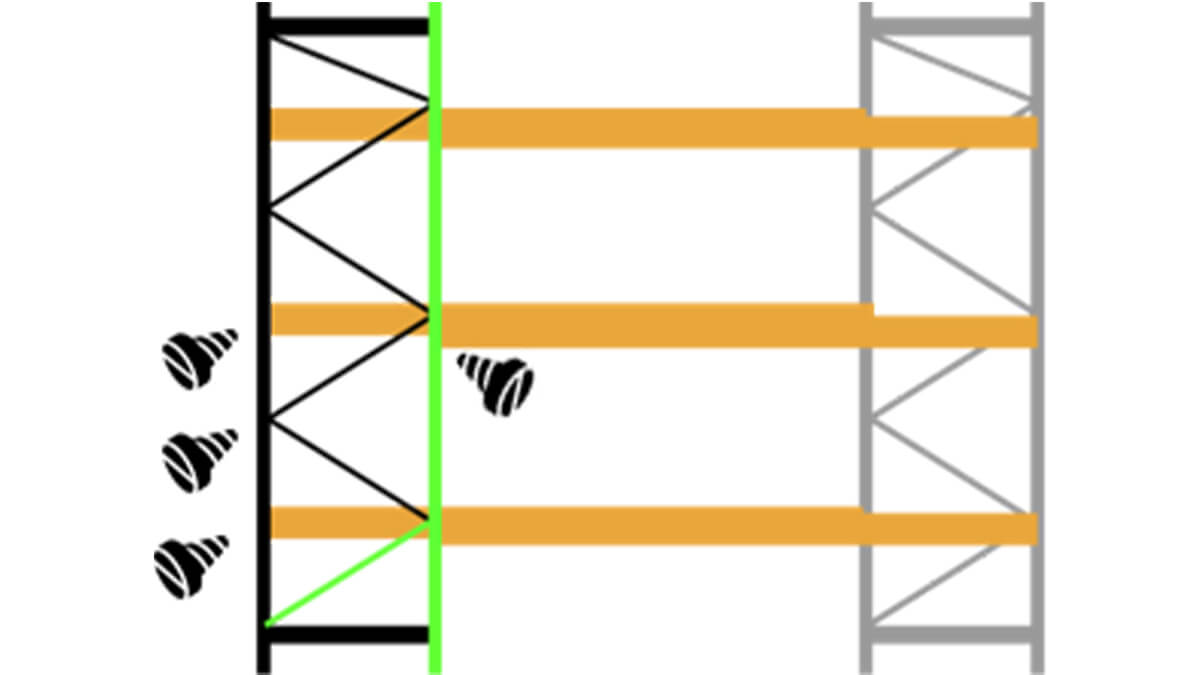
If more than one diagonal needs to be replaced, the procedure described must be carried out sequentially. Never remove more than one racking diagonal at a time.
Replacing a racking upright or frame:
If you have to replace an upright or frame of an industrial racking system, please contact the racking manufacturer directly.