A Tailor-Made Storage Solution Designed to Support ASCO FOODS’ Growth
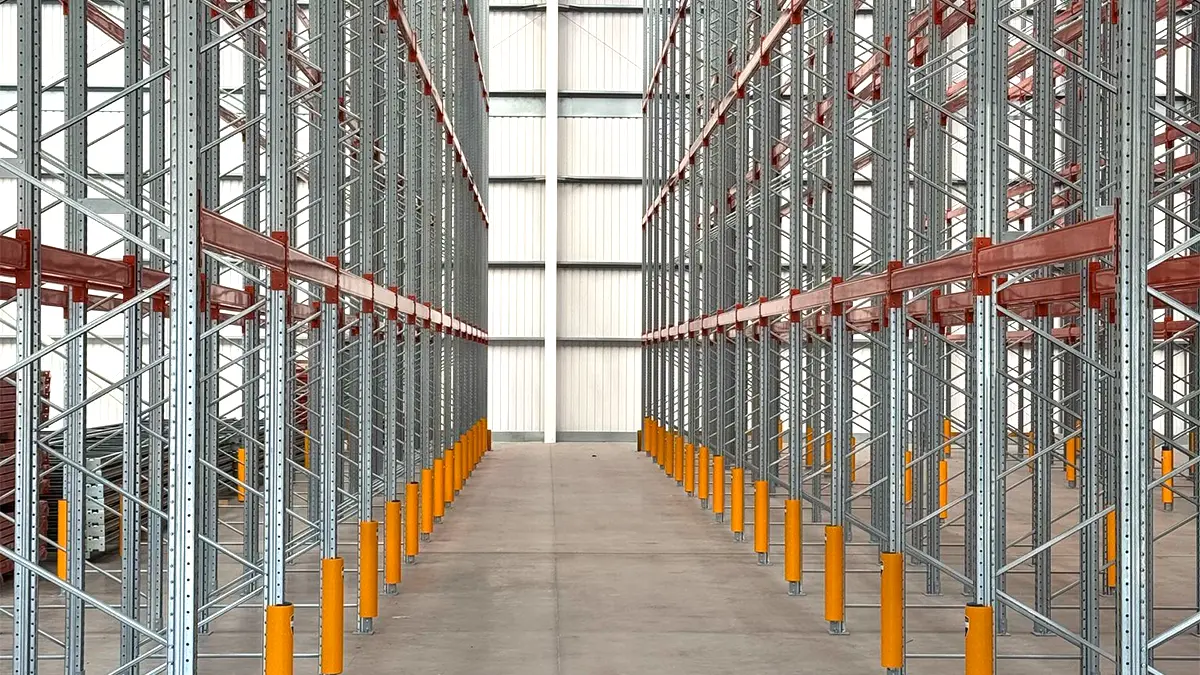
- Featuring high-rise pallet racking and a capacity for over 5,500 pallet positions, AR Racking has contributed to the optimisation of Asco Foods' warehouse operations.
- The project, carried out by STS Storage Systems at the new Asco Foods facility in Thame, stands out for its swift implementation, temperature-controlled zones and seamless adaptation to the customer’s expanding logistics demands.
Facing the challenge of rapid growth and the need to relocate its operations, Asco Foods, a major UK importer and wholesale supplier of South East Asian ambient and frozen foods in the UK, entrusted a comprehensive storage solution to support their new logistics platform. The project, delivered by STS Storage Systems with technical support from AR Racking, has equipped the new Thame warehouse with capacity for over 5,500 pallet positions, maximising space usage and boosting operational efficiency.
Asco Foods had outgrown its previous facility, prompting not only a move but the need for a scalable solution that would maintain service levels and minimise downtime. The new distribution centre, covering over 51,000 ft², required a strategic storage design to accommodate growing volumes and a diverse product range, many of which require temperature-controlled environments.
“Our growth meant we needed to act quickly but strategically. The storage solution implemented has enabled us to relocate seamlessly while improving inventory management and stock visibility, making the most of every cubic metre of the new warehouse,” said Sunny Chadha from Asco Foods.
The system selected was a high-rise Adjustable Pallet Racking installation (11,500 mm) covering both ambient and chilled areas. The flexibility of the design, adapted to the pallet type used (1000 x 1200 mm), was crucial to meeting tight project deadlines, with the customer eager to start operations quickly to avoid additional rental costs.
The project was completed in two phases: the first in January and finalised in May, with all timings strictly adhered to. Close coordination between AR Racking and its official distributor, STS Storage Systems, ensured a smooth and efficient execution.
“At AR Racking, we applied our structural design expertise to tailor the system to the customer’s technical and scheduling requirements. The close collaboration with STS’s engineering and installation team was key to delivering a robust and scalable solution,” said Gonzalo Crovetto, Project Manager at AR Racking.
Richard Tyrell, Project Lead at STS Storage Systems, added: “The success of this project came down to fully understanding Asco Foods’ challenges and translating them into a flexible, efficient, and high-quality solution. Working with AR Racking gave us the confidence to meet every commitment to the customer.”
With this new infrastructure in place, Asco Foods has strengthened its logistics capacity and is now well positioned to support its continued expansion in the UK market and beyond. A solution designed for today, with a clear vision for the future.