The development and transformation of logistics in recent years is unstoppable, mainly due to changes in the behaviour of society and the growth of e-commerce.
In this context, the picking or order preparation processing in the warehouse is of paramount importance in the supply chain of companies. We analyse below the concept, applications and advantages of the type of picking known as “wave picking”.
What is wave picking?
Wave picking is a picking strategy for the warehouse that consists of grouping orders by common logistics criteria assigning a set period to their preparation.
This order grouping criteria can be by end customer, type of carrier, volume or size of the load, delivery periods, etc.
This order preparation process is therefore carried out in waves, hence the term for this type of picking.
Differences between wave picking and batch picking
The terms wave picking and batch picking are very closely related, they have many common characteristics and are even sometimes used interchangeably.
Their main common characteristic is the grouping of goods by criteria which helps to optimise time and the distance covered in the warehouse. In fact, in many cases there are companies that carry out both batch picking and wave picking.
Batch picking means that the operator collects on their route various units of the same reference which are later transferred to a consolidation area where they are grouped and organised into different orders.
In wave picking, this collection of the goods in waves is planned according to the chosen criteria, in a set time and with an assigned operator.
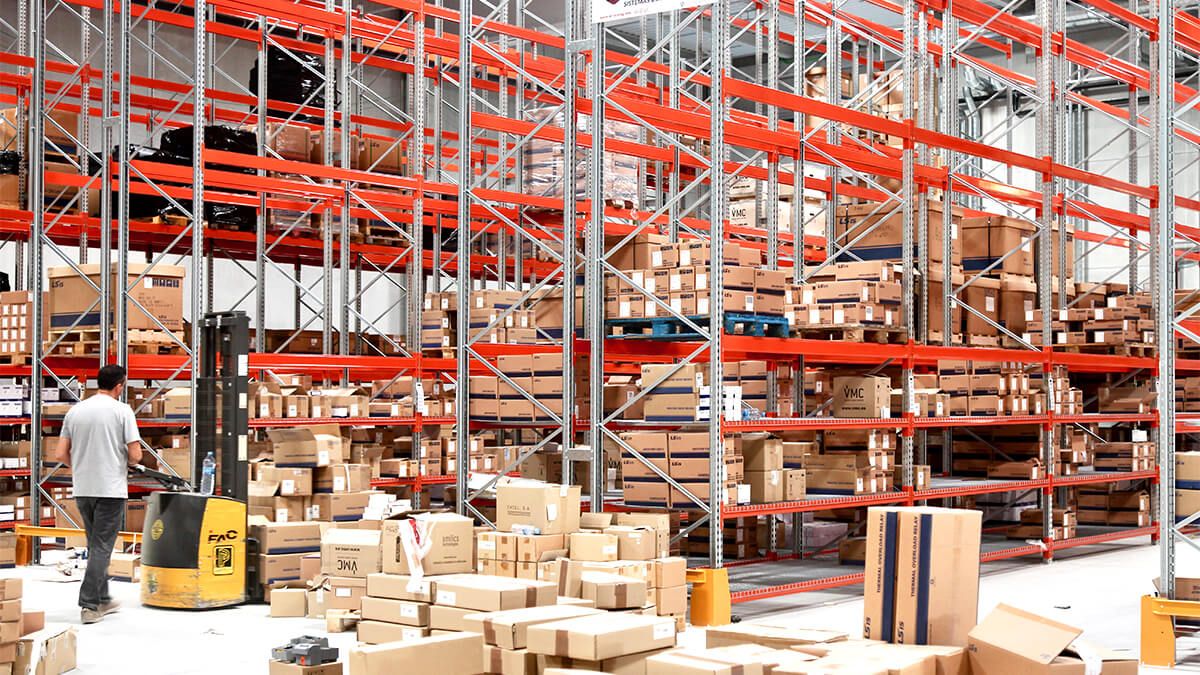
Wave picking operation in a warehouse
The wave picking operation is the first step in defining the criteria by which the orders are grouped, which as indicated above may vary significantly according to the company’s needs. These criteria are: from their grouping by the carrier who will be responsible for their transport, the end customer who will receive the goods, the size or volume of the products, the delivery periods of the different orders, etc.
Once the grouping criteria has been defined, a time period must be assigned for order preparation. This time period must be around 30 minutes and 4 hours for each wave, always depending on the type of warehouse, its size, distribution and type of product.
The operator responsible for each wave picking must also be defined, as they will collect all the goods on the same route and in the time stipulated above.
The order preparation process is finally completed with the packaging and consolidation of the orders, and organising their preparation for shipment from the warehouse. The operator may also prepare and package the orders in the same shuttle as they collect them, although generally this makes the process less efficient.
Main advantages of applying wave picking
Despite being a complex system that requires meticulous pre-planning, wave picking has clear advantages for its application in a warehouse or distribution centre:
Time optimisation
One of the main advantages of wave picking is optimisation of order preparation times. Goods collection times are reduced by completing the picking in the same route or wave.
Reduction of distances covered by operators
When planning this wave collection system, the operator must avoid having to make unnecessary journeys repeatedly to prepare each order. The route followed in each wave is optimised to minimise distances covered, reduce journeys in the warehouse and therefore reduce order preparation times, reduce traffic and increase safety inside the warehouse.
Improved stock flow in the warehouse
With wave picking exhaustive control over the collection and preparation of each product in the warehouse is maintained, thereby ensuring a correct stock flow and a good collection, replenishment and order shipment process.
Maximum number of goods to collect
The organisation and distribution of the unit load in the warehouse by this method helps optimise the collection of each operator’s goods, since they not only collect products associated with an order, but also those defined by the assigned grouping criteria.
For wave picking, it is important to remember that the subsequent product consolidation grouping process will be key for preparing order shipment in the warehouse. This is perhaps one of the negative points to consider when implementing a wave picking process in the warehouse.
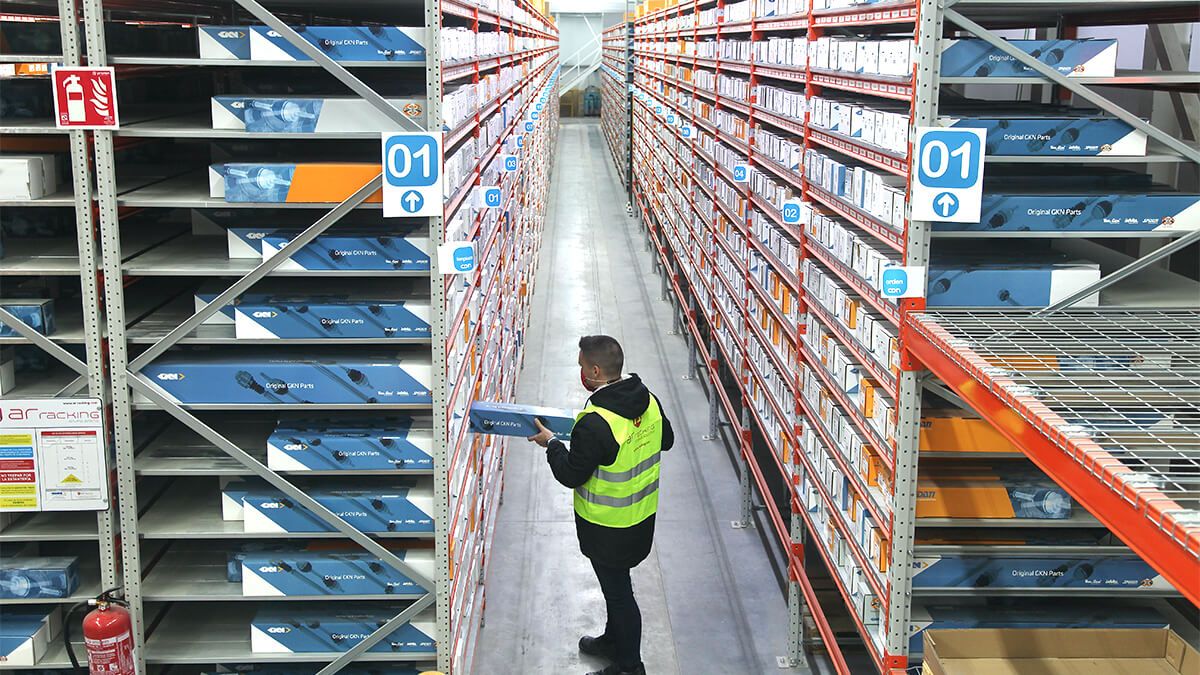
In what warehouses is wave picking applied?
As with all management methods in a warehouse, both the specific characteristics of the company and the warehouse need to be considered to decide whether it is the right system.
In all systems the aim is to achieve greater productivity in the logistics operation of the warehouse, to improve flow and ensure that there are no imbalances in the workload.
In the case of wave picking, considering its strengths and weaknesses as a system, it is particularly useful when applied in warehouses with the following characteristics.
Wave picking is an ideal system for warehouses that have a high number of product references with multiple orders per day, i.e., fast-moving inventory.
The wave picking system will work better the higher the percentage of fast-moving inventory in the warehouse. If most of the products are slow-moving generally it is more interesting to apply a conventional picking system, such as pick to box.
It is especially recommended in very large warehouses, with light unit loads and that can also be easily accessed by the operator. When implementing the wave picking system in a warehouse it is very important to define what type of industrial racking will be installed, to ensure that the picking system chosen facilitates the manual loading and unloading process of the goods quickly and in an orderly manner.
Being a complex picking system that requires planning, it is advisable to implement it together with a warehouse management system (WMS), that facilitates and ensures the organisation and planning of each of the waves and subsequent order consolidation.
In light of all these variables, it needs to be decided whether to opt for wave picking or have a waveless warehouse.