100% Automated Production Centre
AR Racking Industrial Shelving Factory The AR Racking Production Centre is one of the most advanced automated industrial shelving factories internationally.
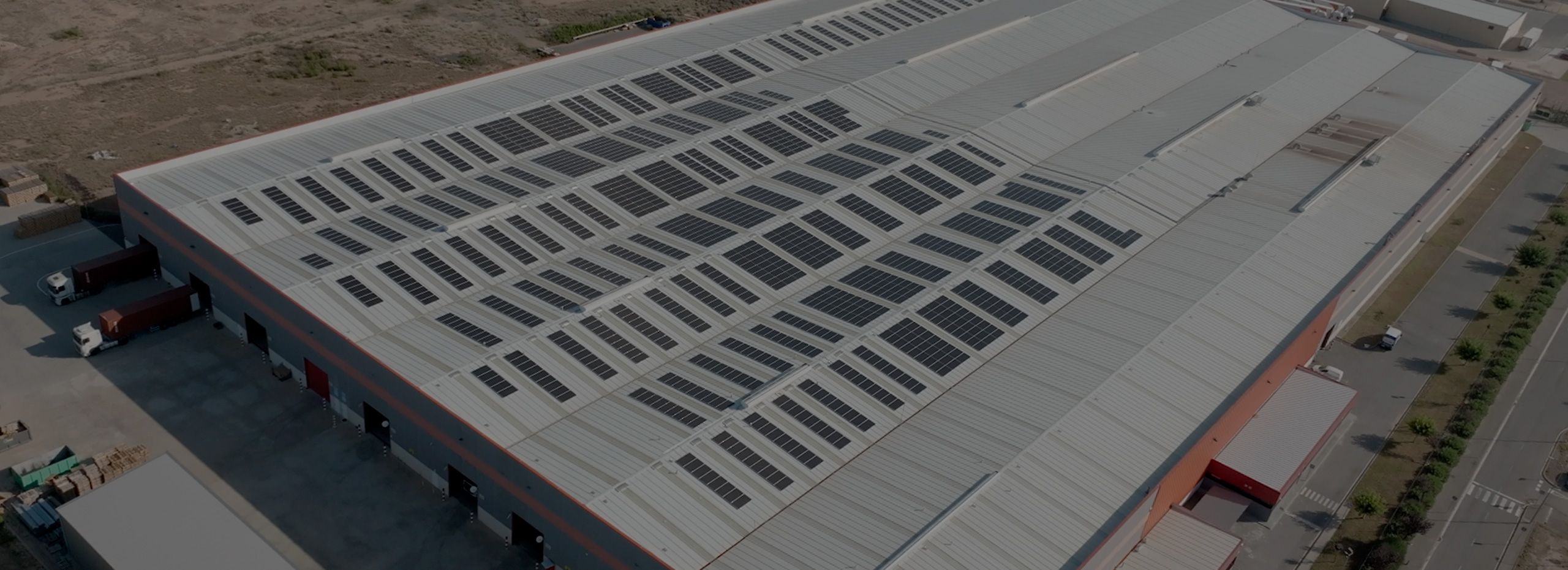
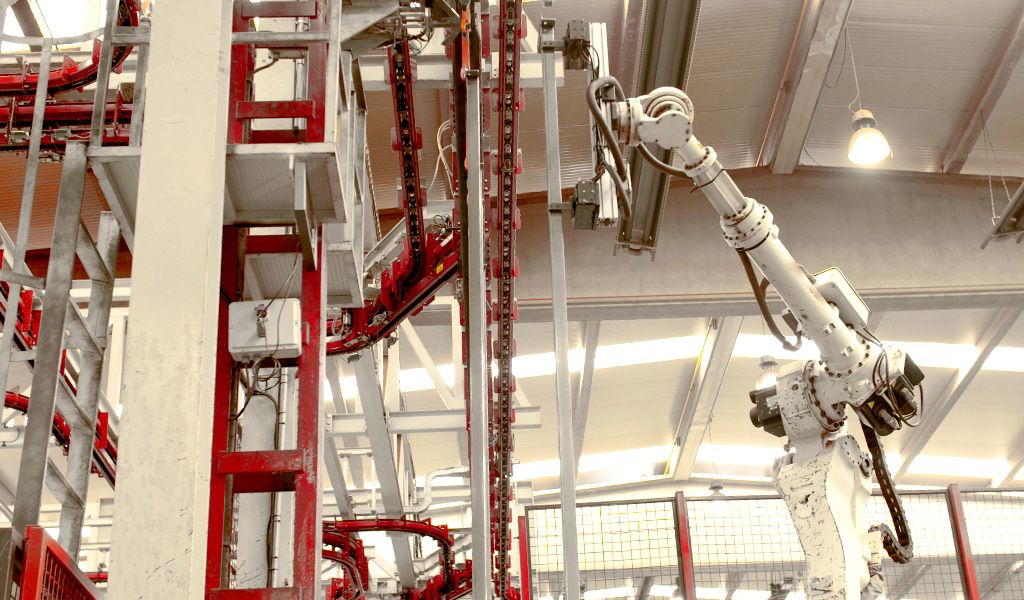
Automated Industrial Shelving Factory
The automated production center of AR Racking, located in Tudela, Navarra, stands out as one of the most advanced factories in Europe and internationally in the manufacture of industrial shelving.
This modern center is a clear example of AR Racking’s commitment to technology and innovation, allowing us to meet the highest international quality standards.
Our plant in Tudela is equipped with state-of-the-art machinery and automated production systems that ensure excellent efficiency and precision at every stage of the production process.
From the selection and handling of raw materials to the final product finish, each stage is carried out with rigorous quality control.
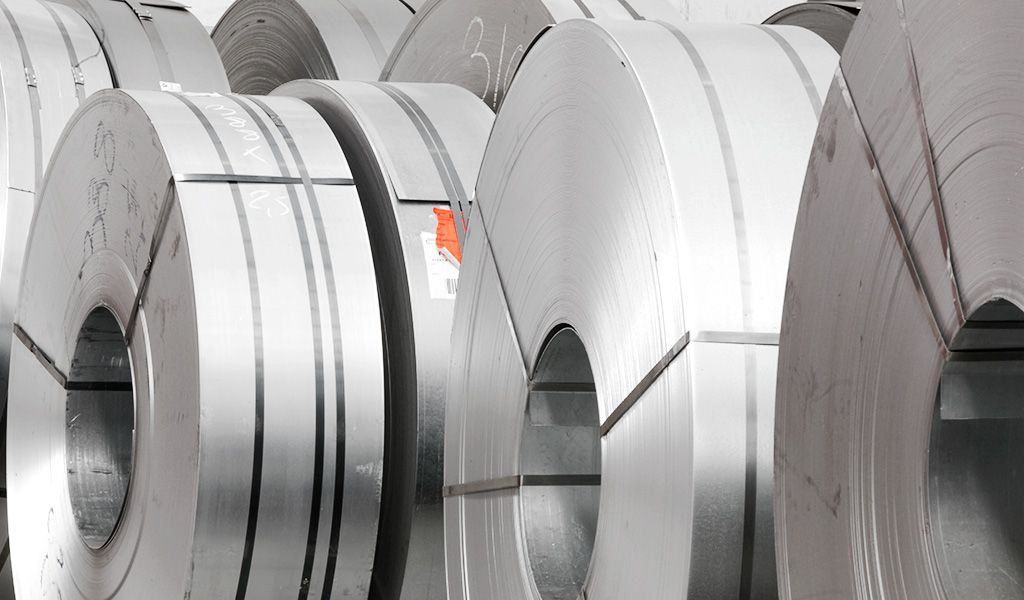
International Quality and Excellence
At AR Racking, our commitment to the highest quality and excellence is non-negotiable, and we apply these standards to every phase of the production process.
As part of the steel group Grupo Arania, with over 85 years of experience in the sector, we are experts in steel treatment.
We use different grades of steel according to international standards, such as EN 10025, EN 10346, EN 10149, and EN 10139, ensuring that each component of our shelving meets the most demanding market requirements.
Traceability is another crucial aspect of our production center, for which we have an innovative system to identify each piece with a unique serial number, facilitating its tracking and quality control throughout the production cycle.
How are our industrial storage systems manufactured?
In the manufacturing process of our industrial shelves, we use the most advanced technology to ensure high-quality products that meet the strictest safety standards. The following is an in-depth explanation of each step in the manufacturing process:
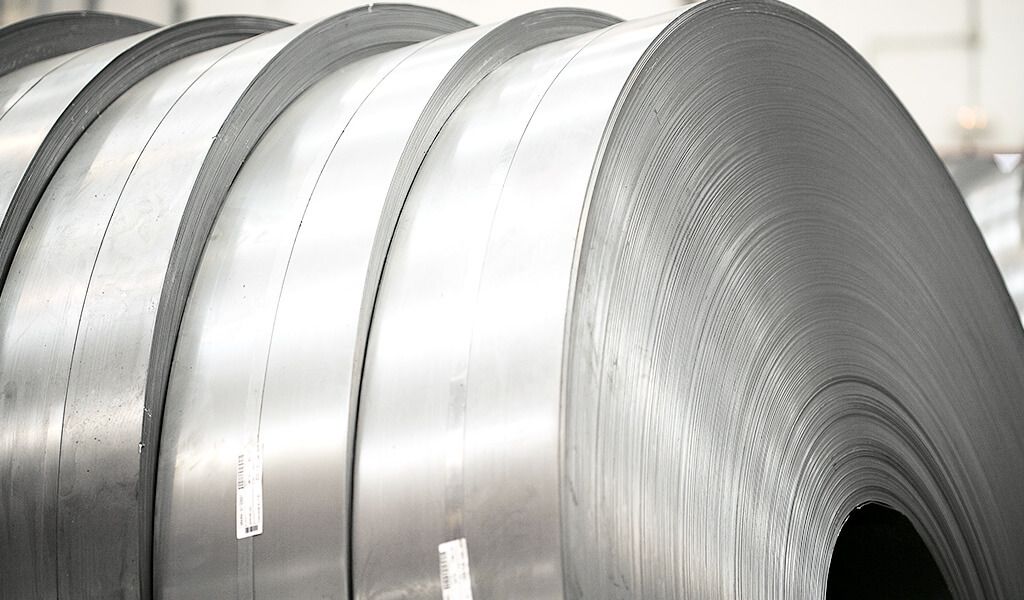
Raw Material: High-Quality Steel
Knowledge and selection of raw materials are key. As part of one of the largest international steel business groups (Grupo Arania), we have extensive experience in choosing the highest quality steels for our industrial shelving.
We use different types of steel according to standards:
- EN 10025: Hot rolled products of structural steels.
- EN 10346: Continuously hot-dip coated steel flat products.
- EN 10149: Hot rolled flat products made of high yield strength steels for cold forming.
- EN 10139: Cold rolled uncoated low carbon steel narrow strip for cold forming.
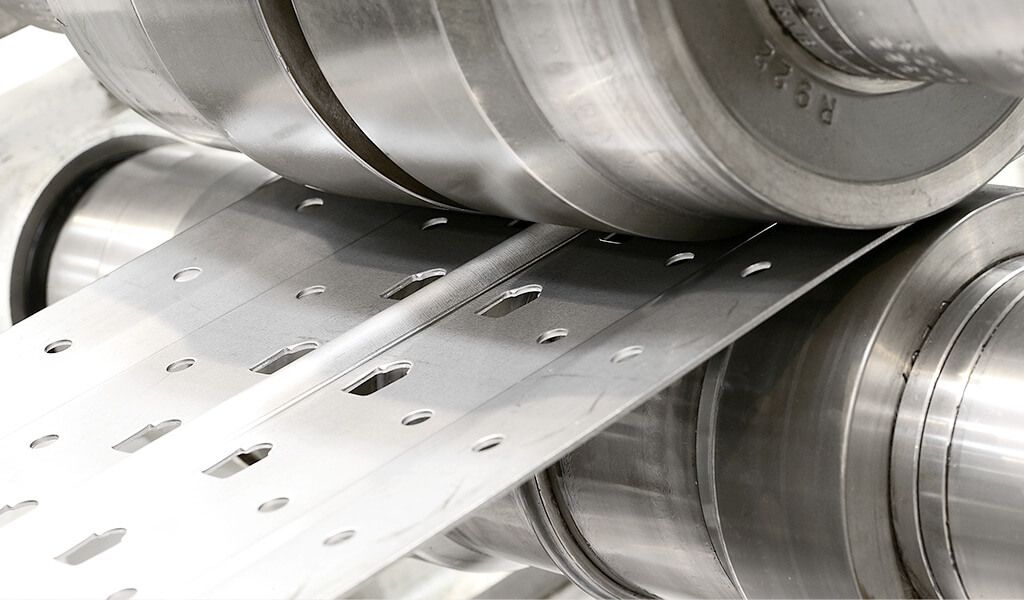
2. Cold Profiling Process
The cold profiling process of steel is the initial phase in the manufacture of our industrial shelving. This method transforms steel coils into structural profiles through a cold deformation process, which is carried out without preheating the material.
Cold profiling begins with feeding steel coils into our advanced profiling machines. These machines have a series of rollers specifically configured to shape the steel, ensuring that each profile meets the exact dimensions and quality standards required. During this process, strict quality controls are applied to verify that critical measurements are maintained within established parameters.
This method also improves the mechanical properties of the steel, increasing its strength and durability.
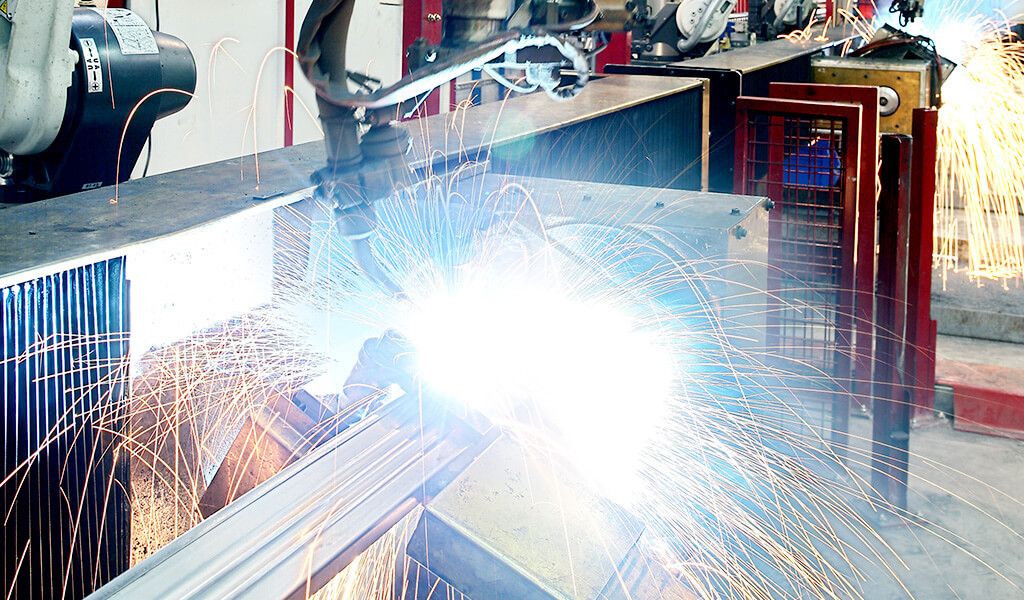
3. Welding Process
Our automated welding system allows for precise and consistent welds between the beam profile and the connector, eliminating variations that could compromise the structural integrity of the shelving. Automation not only increases efficiency but also ensures that each weld is performed with the same level of accuracy and quality.
All welded parts undergo a thorough final inspection to detect and discard possible defects. This process includes visual inspections and non-destructive tests to ensure the integrity of the weld.
We strictly comply with ISO 3834-2 regulations, which establish quality requirements for the fusion welding of metallic materials. This certification guarantees that our welding processes meet the highest international standards of quality and safety.
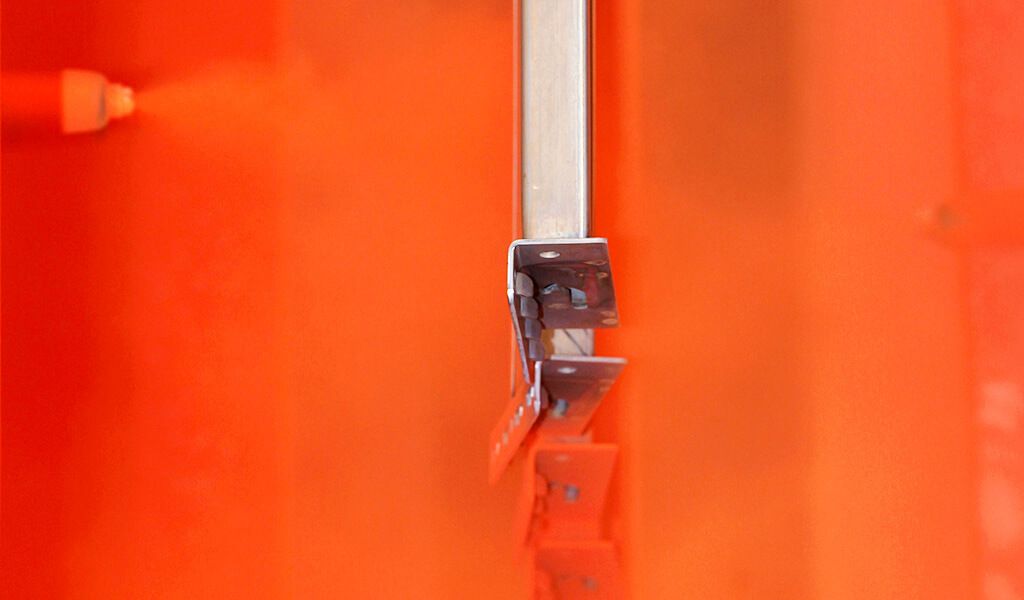
4. Shelf Finishing: Painted or Galvanized
Beams, uprights, and frames are adapted to the needs of the customer and environmental conditions.
For this, in our production center, we manufacture the elements of industrial shelving with different types of finishes:
- Pre-galvanized: Ideal for elements such as uprights that are more exposed to abrasion, ensuring optimal resistance.
- Painting: Beams can have a pre-galvanized and painted finish to improve visual contrast and facilitate the operator’s work. The process includes a prior nanotechnology treatment, electrostatic application of epoxy-polyester, and oven curing, ensuring maximum quality and fire resistance according to UNE EN ISO 13501.
- Hot-dip galvanizing: Provides high resistance to oxidation and corrosion, especially in extreme conditions.
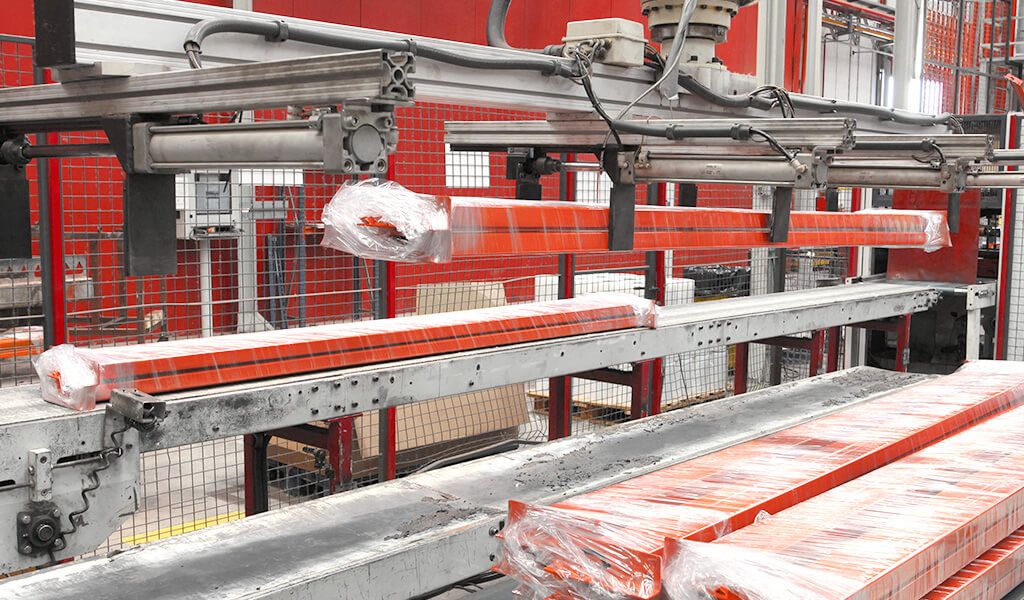
5. Packaging Process
In this final phase, uprights and beams are automatically packaged to ensure uniform protection against impacts during handling and transportation.
Each package is wrapped and secured with polyester straps for storage and delivery.
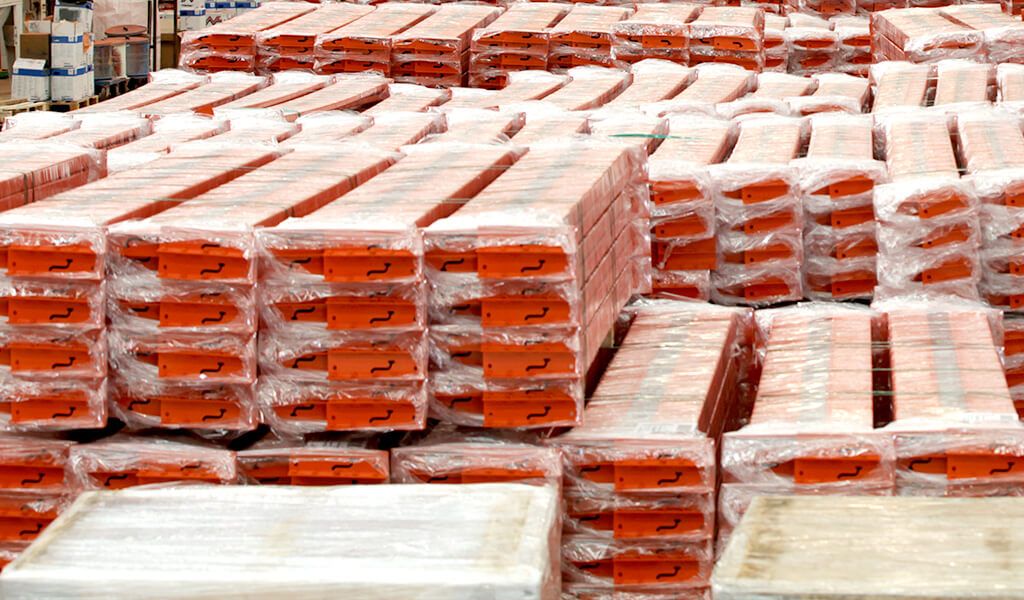
6. Final Product Storage
The finished product is stored until shipment in our facilities under the best maintenance conditions.
We have a large manufacturing capacity and available stock to serve our customers internationally.
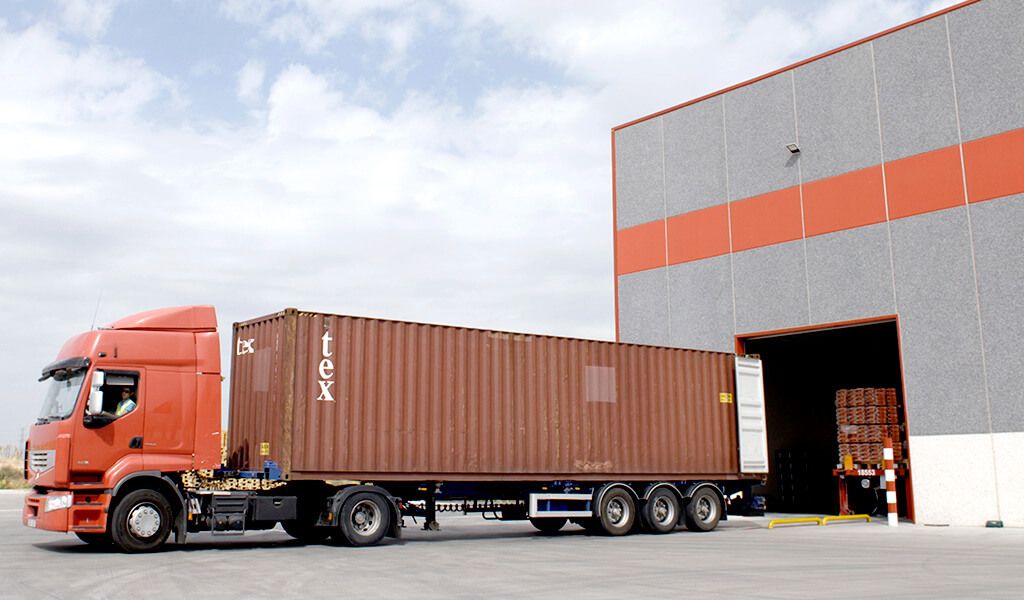
7. International Shipping with the best Lead Times
From our production center, AR Racking is committed to shipping our products with one of the best lead times in the market. We guarantee fast and efficient delivery times, ensuring that orders to equip our customers’ warehouses arrive at their destination on time.
Thanks to our optimized logistics and a well-coordinated distribution network, we can offer an international shipping service that meets the highest expectations of our customers worldwide.
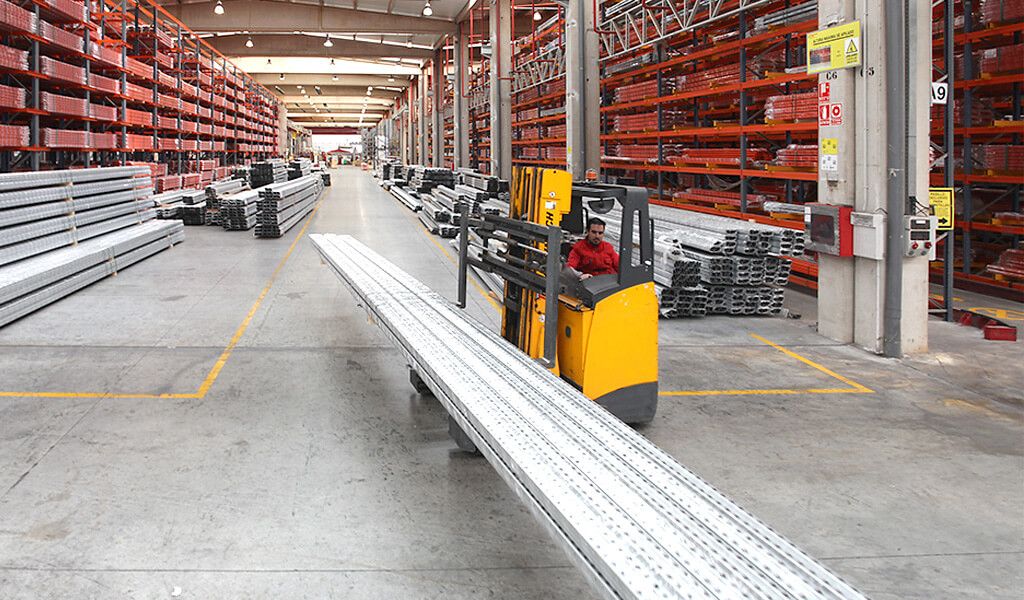
Production capacity of 100,000 toness
With a production capacity exceeding 100,000 tonnes annually, AR Racking stands out in the international market as one of the leading manufacturers of industrial shelving.
This extensive production capacity allows us to meet the demand of a wide range of industries worldwide. With a presence in over 60 countries, our storage solutions are tailored to the specific needs of each customer, ensuring efficiency and space optimization in warehouses.
The capacity to serve an extensive global market highlights the dependability and distinction of our solutions.
Additionally, at AR Racking, we continue to invest in advanced technology and efficient production processes to maintain market leadership with a combination of high production capacity, global reach, and a focus on quality.
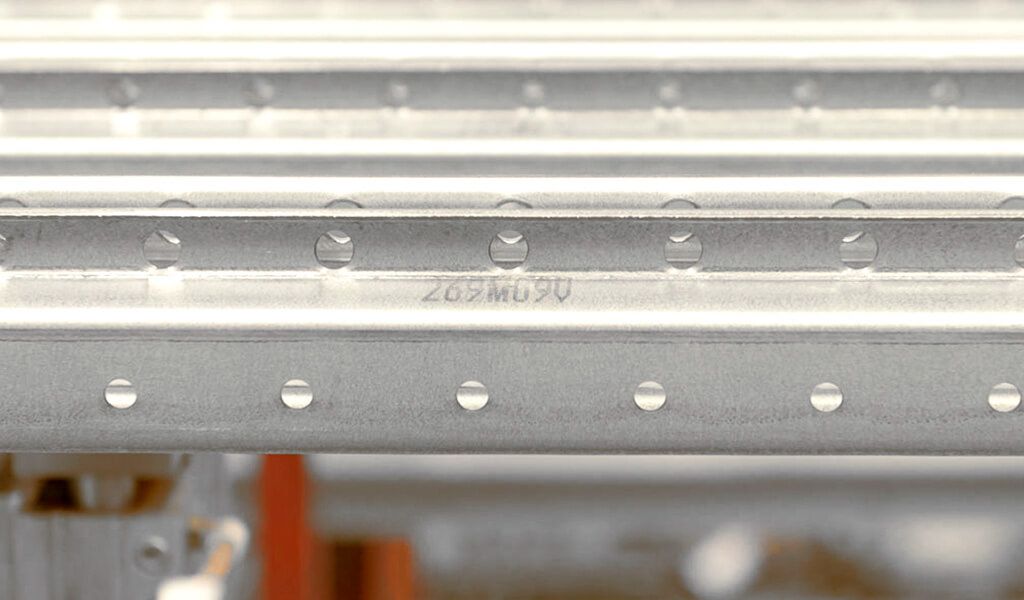
Traceability system applied to manufacturing
At AR Racking, we have an innovative traceability system for our industrial shelving, ensuring the quality and thorough control of our products.
This system, in operation since 2016 at our production center, focuses on tracing the uprights and beams, fundamental elements that make up the structures of our metal shelving.
The implementation of the traceability system is carried out by laser marking an identifying serial number on the beams and uprights during their manufacturing process. This serial number provides detailed information about the entire production process of each piece, allowing us to document its origin without needing to keep the original package label.
Thanks to this advanced system, we can identify each piece, its design, and the materials used in its manufacture, including raw materials, paint, and consumables. The laser marking is done in the final stages of the production process, ensuring that the paint or galvanized finish of the pieces is not damaged.